Why is production and machine data acquisition even necessary? Companies, factories, production lines, machines or plants have one thing in common. Generating a positive return is only possible if smooth operation with the highest possible utilization is ensured. Any downtime, whether minor or significant, will inevitably result in financial losses.
At management level, it is considered a matter of routine and of course regulated by legal provisions that, for example, accounting is required. On the production level, in the operative areas of many companies, the processes are often controlled using a mix of gut feeling, estimates and experience. Such an arrangement requires professionals with a lot of expertise, experience and often a great deal of commitment to handle sudden inconsistencies in the process. Seen the other way round, the success of the business depends on how well and for how long these skilled professionals and their exceptional commitment are available to the company. An incident may mean a lockdown in the entire process or require a lot of financial effort to get back to the desired results.
Of equal importance is the data exchange between the company’s management and production levels. If this is done on the basis of estimates and past experience, detailed capacity utilization control and cost-oriented planning or calculation is difficult to carry out. A solid database for operating data provides current actual data from the process, makes procedures transparent and ultimately creates knowledge – digital production knowledge. And knowledge is capital, which in turn can be used more effectively than in coping with “provoked” failures.
What Can Be Achieved With PDA?
A modern production data acquisition system with suitable interfaces automates data acquisition, includes the machine data and serves as a connective platform to link the company management level with the production level. The constantly available database built on real actual data enables decisions to be made in the “now” and offers very good data quality for analyses or future forecasts. Where in the process chain can effectiveness or efficiency be increased? Production data acquisition makes the process flow transparent and immediately reveals weak points. Based on the recorded data values, a wide variety of evaluations can be carried out in multi-layered reference variables such as time scales or locations. Reporting such as shift, daily, weekly or monthly reports with the usual key figures on performance, quality up to the overall plant effectiveness in process chains is digital and automated.
As long as everything runs like clockwork, it is not absolutely necessary to react and rearrange the process. This changes very quickly if unforeseen events such as machine breakdowns, lack of work or a large order put a strain on the process flow. In such cases, decisions must be made quickly and reliably. With digital production data acquisition, the actual key figures and production performance are perfectly clear. Wherever something has to be compensated for, it can be controlled in a targeted manner, for example by deploying personnel. For the future and the production processes of tomorrow, automated production data acquisition is absolutely essential. Times are changing, production must be able to handle smaller batch sizes, products are becoming more individual and have to be available faster.
Today, we are already talking about automated workflows and interrelated production lines (cyber-physical systems), whose processes are even supposed to regulate themselves. Numerous technologies such as IoT platforms, digital twins, artificial intelligence and cloud applications are available for this purpose. These technologies require data as a basis for their application. Cooperation between man and machine requires collaboration, as provided by the corresponding interfaces for digital data acquisition.
Where Does It Make Sense to Digitalize and Automate PDA?
Every investment and change in organization must bring improvement and appropriate benefits. The investment in an automated production data acquisition is worthwhile if:
- data recording is required by law or regulations
- business decisions should be based on actual process data
- planning reliability is to be improved
- disruptions in operation can be reduced
- there is a desire to improve the production processes
- the operating resources and auxiliary materials used are to be employed in a resource-efficient manner
- the productivity of machines or personnel is to be increased
- the quality of production is to be improved
- customer satisfaction can be increased
- it is reasonable for the company controlling or quality management for other reasons
These are usual reference points from practical application. The motivation to introduce automated production data acquisition can vary greatly. Basically, the focus is on where and to what extent the collection of data values and acquisition of information can support the process now or in the future.
How can modern technologies contribute to successful implementation?
The step of saying “Yes” to production data acquisition immediately raises the question: “How and with which system should this be implemented?” Modern PDA systems like digifai control follow a web-based approach. The advantages are obvious. The application is available on any internet-enabled device without the need for complex installation.
The data sources such as machines, controls and sensors can be integrated quickly and cost-effectively into the PDA system using so-called IoT Gateways as an interface between hardware and software. Manual entries and hand recordings can be made directly in the browser application via online forms. The data source and user administration can be done directly in the application via an administrative access. No special programming skills are required.
The whole system is secured by multiple layers and access takes place via a secure Internet connection with password protected user login. Data processing requires functions that generate information from data value histories. For example, trend analyses, triggering to limit values with different escalation levels, automated calculation of key figures and the recording of measurement series are, together with digital reporting, a must in modern production data acquisition.
To trigger automated notifications, alerts and the start of automated workflows, the PDA system should include these functionalities as digifai control does. Due to WEB technologies an easy and fast integration is guaranteed, because the usually pre-existing network infrastructure “Internet” is combined with cloud functions.
Digital Alone Does Not Yet Mean Collaboratively Available and Mobile!
The key to acceptance of automated production data acquisition is availability and ease of use at all process levels. It therefore makes sense to provide production data acquisition based on cloud technology. In addition to availability, this approach also brings the advantage of mobile process monitoring. Like digifai control, the platform for production data acquisition should be set up as an IoT solution. With the concept of collaboratively exchanging information with external systems and employees. Local data silos on the other hand usually do not have the desired effect.
Tips for Implementation
The requirements for production data acquisition can be very different. Likewise the everyday process practice must be considered in the system selection. The first step, however, is to determine which data sources, machines, plants, sensors are relevant for production data acquisition. What information about the process is to be obtained and via which interfaces will the data be made accessible. For this purpose it is advisable to build up your own expert knowledge or to seek external advice. In order not to end up not realizing PDA projects because of their assumed complexity, a path of small steps is recommended. In suitable test or pilot plants the functionality and practical suitability within your own process can be explored. A pilot phase helps to clarify the requirements for a roll-out and the anticipated costs and efforts.
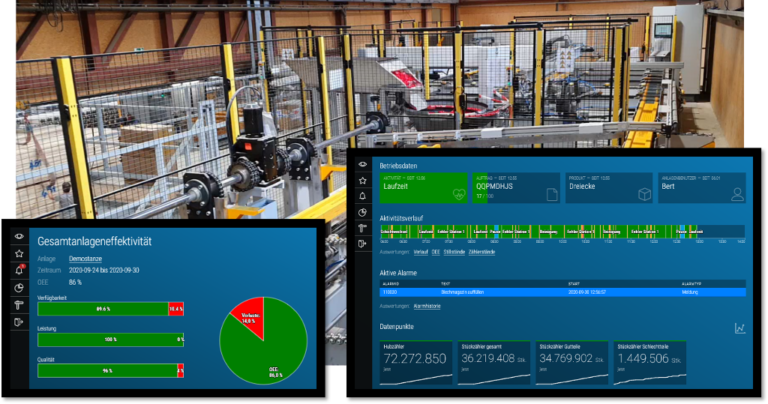
Practical Example – It’s That Simple!
The activity of an existing machine is to be recorded. The machine itself has no digital interfaces. It does, however, have operating and error indicators. The signal of the indicators is connected to an IoT gateway.
Solution:
- IoT Gateway with power supply and LTE modem
- Digital input module
- Auxiliary contacts if necessary
After commissioning, the data is recorded continuously and manual recording is no longer necessary. The “digital” operating display records the operating hours and interruptions due to errors. The machine operator can record the cause or the type of malfunction online in digifai control.
Machine data acquisition made easy!
// Product
Implementing production data acquisition quickly and easily with the IoT Platform control.
