Control Engineering
// Field of Application
Advantages for Control Systems
// Application
twin in Use
With twin, digital twins of real machines and systems can be created in an instant. Connected to the real controller, they respond exactly like the actual machine in reality. Thanks to a physical real-time simulation, material transport and the behavior of actuators and sensors are realistically displayed. The advantage? For example, you can design, program and virtually commission your control software on the virtual machine.
The digital twin is given realistic properties by entering the physical qualities of components, actuators and sensors. Using the stored algorithms and the physical calculation, twin simulates how well the program software of the control system interacts with the mechanics of the machine. Motion sequences and their consequences, such as collisions, become visible in real-time, independent of location and hardware. Having the major advantage that everything happens in the virtual world and no real damage is caused.
twin facilitates the cooperation of several commissioning engineers. The virtual model can be reproduced as often as required and can be selectively divided into segments for teams.
The virtual environment allows selective and arbitrarily repeating test phases even in complex systems or processes without affecting the hardware development. Early detection of errors and continuous optimization before final commissioning leads to an increase in software quality.
twin decentralizes a substantial part of the commissioning on site. Virtual commissioning reduces the lion’s share of travel expenses and minimizes commissioning times at the end of the project, which automatically means shorter downtimes in the customer’s production plant. In summary, virtual commissioning optimizes machine setup. twin reduces the risk of extended commissioning times and results in satisfied customers due to short interruptions in operation.
In the event of an upcoming modernization of existing systems, twin supports the development by first virtually testing the adaptation of the control software and only then installing it on the production machine.
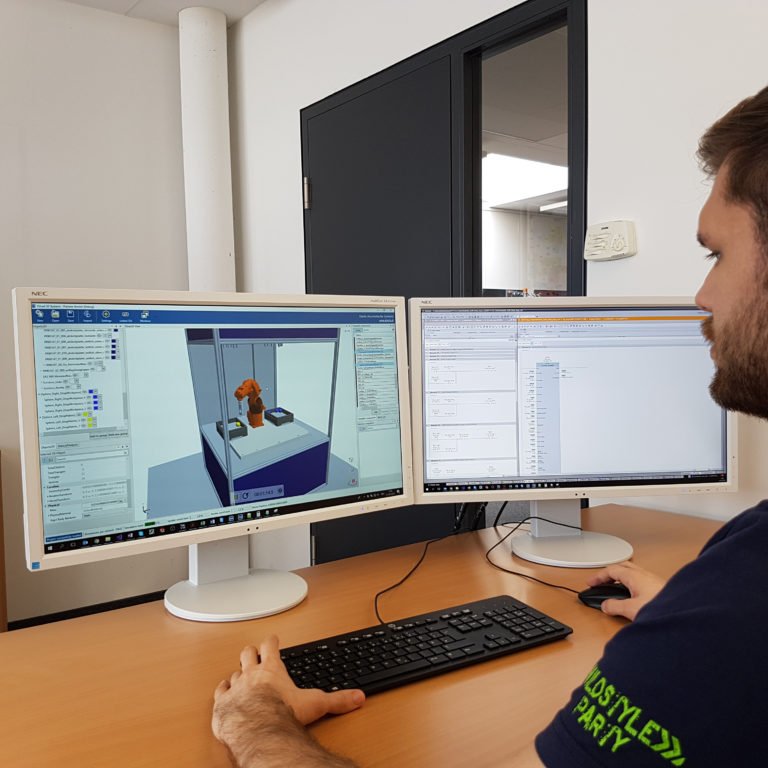
The virtual commissioning on a digital twin is independent of location and hardware.
// Examples
Application in Detail
This application video demonstrates the virtual commissioning of a robot cell. Parallel to the mechanical production of the cell, sequences are already being tested and optimized with twin. And the best thing about it: We are using the real control system!
This is a Bin Picking robot cell using twin. A master computer, a PLC and a robot controller interact with the digital twin. Virtual cameras detect objects and virtual grippers allow parts to be moved around. The path planning of the robot is carried out in the host computer using a sophisticated algorithm. The simulation of physical effects with twin enables realistic testing of the entire process
The application video shows the commissioning of a conveyor line. Frequency converters and conveyor belts are controlled by a PLC according to the feedback signals of the light barriers. One and the same control program for the digital twin as well as for the actual machine built in reality!
// Contact
Get to know us
We help you to digify your systems, to make them intelligent. So you get more out of the data that is available anyway. We will be happy to discuss with you personally how we can help you.
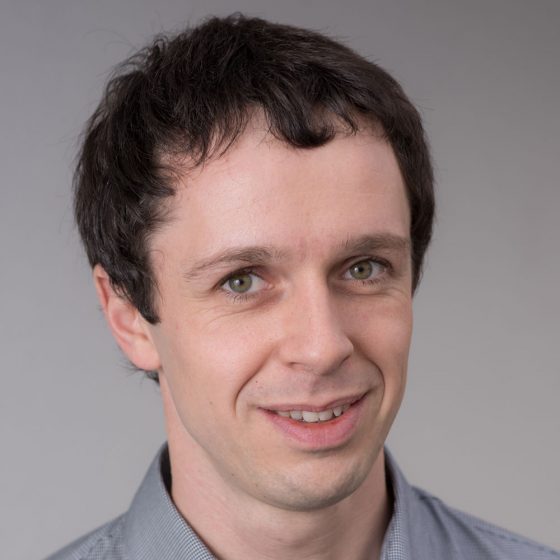
Michael Eberle
Chief Technology Officer
+43 5572 55580 803
michael.eberle@digifai.com
twin
twin creates a digital twin. This allows you to test the controls of your system before the machine is set up.